Practical tips to optimise your machine
Read a number of tips from our technicians below. If you have specific questions about our equipment, please contact us. Should you ever have any issues with your Andy Guest equipment, our repair service is always ready to respond quickly.
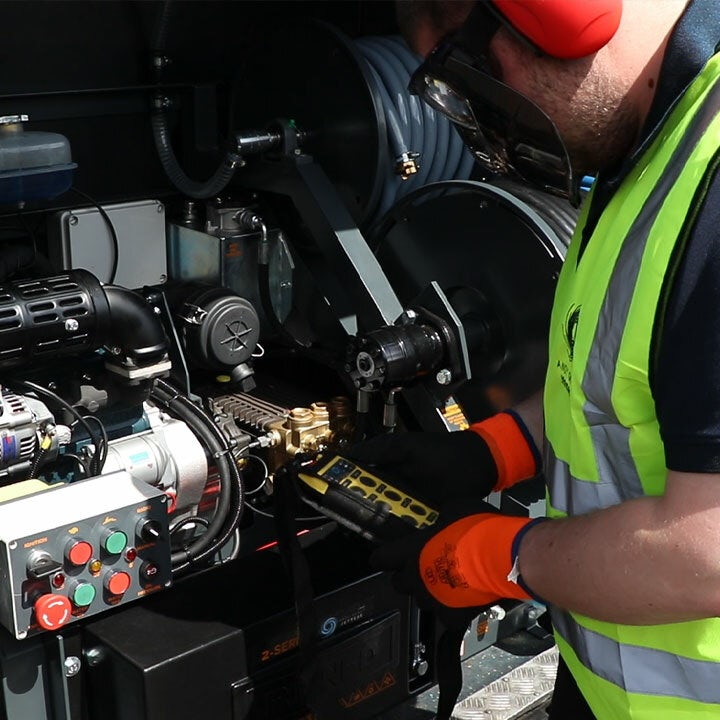
Check the battery regularly
On average, a battery lasts about three to seven years. At low temperatures, the capacity of the battery decreases and the starting resistance of the engine increases, therefore making it more difficult or even impossible to start the jetting machine. Have the battery checked regularly and replaced if necessary.
Switch idle machines to Euro98 fuel
E10 petrol consists of 10% bioethanol, which should be changed when the machine has been idle for a month or more to prevent damage to the carburettor. If the jetting machine is not in regular use, we advise using Euro98 fuel, which is less harmful to the machine’s components.
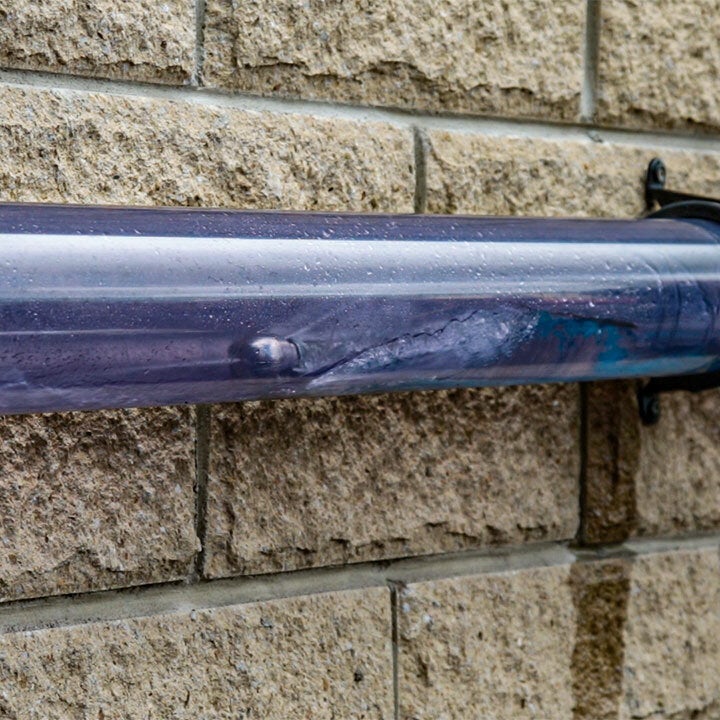
Clean the nozzle spray heads
To guarantee the optimal effectiveness of your nozzles, we recommend that you keep any holes in the nozzles clear from debris. Many contractors choose to use a small drill or special pricker set to clear their nozzles, though other methods are also effective.
Ensure your nozzles rotate properly
Rotating nozzles have a 360° range and are very suitable for cleaning pipes. To ensure that your rotating nozzle continues to rotate properly, we recommend that you regularly put it in a jar of diesel or thin oil to lubricate the moving parts.
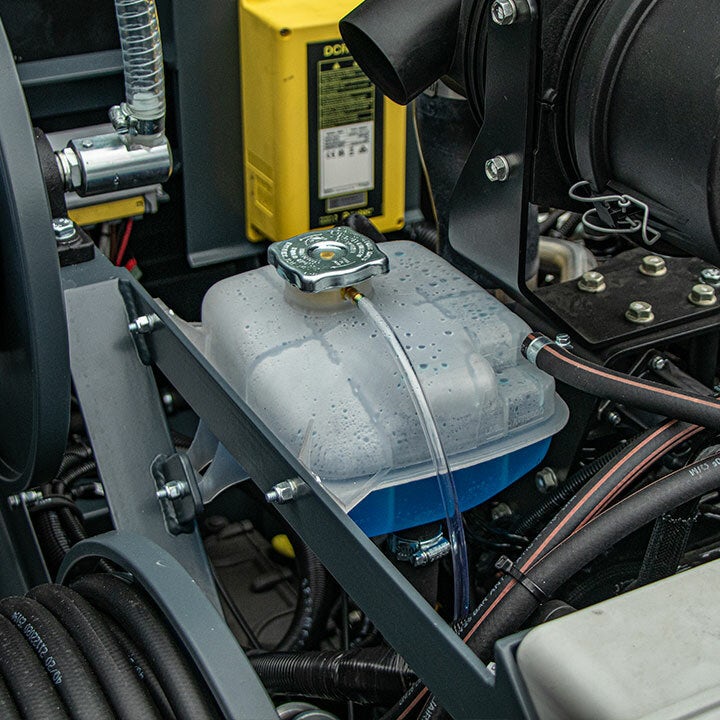
Complete the anti-freeze procedure
Severe winter conditions can seriously damage the pump and other important machine components. Prevent the water tank from freezing by undertaking the anti-freeze procedure. Connect the high-pressure hose to the filling hose and let the system pump the anti-freeze liquid through without pressure. If the anti-freeze runs out during work, let the machine run without pressure.
Prevent damage from saltwater
In winter, de-icing salt is used to combat road icing. The mixture of salt and snow that remains on the road is also known as saltwater. Saltwater has a strong corrosive effect, which can be very detrimental to the bodywork of cars and trailers. Ensure that your car or trailer is properly cleaned on a daily basis to prevent rust from forming on your machine.
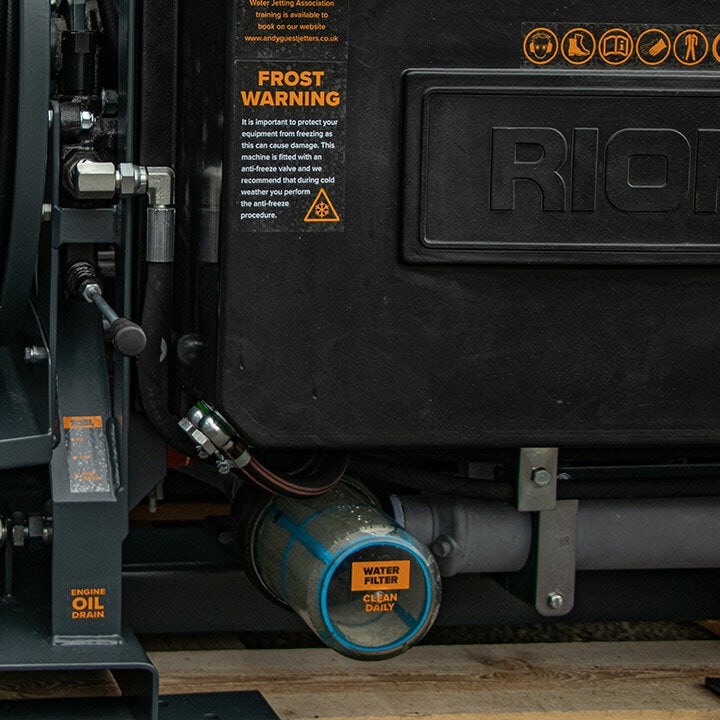
Clean the water filter regularly
The water in the water tanks can be contaminated by algae, lime and cavitation. To prevent this from ending up in the high-pressure pump and hose, our jetting machines are equipped with a water filter. For optimal water filtering, it is important that the water filter is cleaned regularly. Because the water filter is equipped with a transparent filter pot, you can clearly see when it is time to clean the filter. After cleaning, apply a little grease to the screw thread, so that the filter will close easily and become more efficient.
Check inspection equipment for faults
Extend the life of your inspection camera by cleaning and checking your camera regularly. Dirt that is not removed can damage the vital components of your inspection equipment. In addition, check the connections between the camera head and the push-rod cable to identify any damage and detect problems early.
Recommended Maintenance Schedules
We would recommend the following maintenance plans conducted by a recognised service agent using only OEM parts.
ACTION | FREQUENCY |
ANNUAL SERVICE | We recommend that your jetting machine is serviced annually by an AG approved Service Centre. |
Clean water filter | Daily or after high concentration of pollutants |
Clean Engine Air Filter | Every 25 working hours |
Service engine | Every 100 working hours or 6 monthly – whichever is soonest |
Engine Oil Filter | Every 200 working |
Lubricate moving parts | Every 250 working hours or 6 monthly – whichever is soonest |
Cleaning pressure regulator | Every 250 working hours or 6 monthly – whichever is soonest |
Renew pump oil | Every 500 working hours or every 2 years – whichever is soonest |
Check all lines (high pressure/vacuum) including fittings for leaks. Drain regulator of accumulated fuel deposits. Replace spark plugs and set gap. Have lock-off/filter serviced. Have combustion deposits removed if using non-synthetic oil. |
Every 500 working hours or every 2 years – whichever is soonest |
Have regulator disassembled, cleaned, and reset. Have vaporizer disassembled, cleaned, and serviced |
Every 1500 working hours |
Decalcify suction valves | Annually |
Decalcify pressure valves | Annually |
Re-puncture nozzle holes | Every 50 working hours |
Troubleshooting Guide
Engine does not start or stops abruptly
The machine has run out of fuel | Add fuel
Main or secondary fuse blown | Contact your service agent
Battery voltage is too low | Charge or replace
Emergency stop activated | Release the emergency stop on the machine/ remote
The high-pressure pump does not produce the required pressure
Water tank empty | Fill the water tank
Water tank flow valve closed | Open the valve
Water filter clogged | Stop the machine and clean the water filter
Air in high-pressure pump | Allow the machine to run for a few minutes and if the air doesn’t bleed out contact your service agent
Suction valves blocked | Carefully loosen the valves and descale them
Pump drive belt not sufficiently tightened | Tighten the belt; replace if necessary
Suction valves worn out | Contact your service agent
Pressure not consistent
Water level in tank too low | Stop the engine, refill the tank and restart engine
Water supply valve not sufficiently opened | Open the supply valve completely
Water filter clogged | Stop the machine and clean the filter
Pump sucks air | Stop the machine and check all hoses and couplings for leakage
Nozzle clogged | Stop the machine and clean the nozzle (clean the nozzle holes)
Pressure valves dirty or worn | Stop the machine. Check the condition of the pressure valves. Clean or replace them
Pump packings worn out | Stop the machine and replace gasket
Pump drive belts slipping | Stop the machine and tighten the belts
Pump plungers damaged | Contact your service agent
Pressure control clogged or damaged | Contact your service agent
Warning lights after short operation
Battery flat/defective | Recharge or replace battery, Check if the unit is charging correctly, Check battery terminals for debris
Electrical supply appears fine but equipment not functioning
Emergency stop pushed in | Unlock emergency stop
Receiver has no current | Check / replace fuses
No radio connection | Check functions of control lights